जमने के दौरान गैस फंसने से बनने वाली सरंध्रता, कैविटी-प्रकार की असंततता, एमआईजी वेल्डिंग में एक सामान्य लेकिन बोझिल दोष है और इसके कई कारण हैं। यह अर्ध-स्वचालित या रोबोटिक अनुप्रयोगों में दिखाई दे सकता है और दोनों ही मामलों में हटाने और पुन: काम करने की आवश्यकता होती है - जिससे डाउनटाइम और बढ़ी हुई लागत होती है।
स्टील वेल्डिंग में सरंध्रता का प्रमुख कारण नाइट्रोजन (एन2) है, जो वेल्डिंग पूल में शामिल हो जाता है। जब तरल पूल ठंडा हो जाता है, तो N2 की घुलनशीलता काफी कम हो जाती है और N2 पिघले हुए स्टील से बाहर निकलता है, जिससे बुलबुले (छिद्र) बनते हैं। गैल्वेनाइज्ड/गैल्वेनियल वेल्डिंग में, वाष्पित जस्ता को वेल्डिंग पूल में मिलाया जा सकता है, और यदि पूल के जमने से पहले बाहर निकलने के लिए पर्याप्त समय नहीं है, तो यह सरंध्रता बनाता है। एल्यूमीनियम वेल्डिंग के लिए, सभी सरंध्रता हाइड्रोजन (H2) के कारण होती है, उसी तरह जैसे N2 स्टील में काम करता है।
वेल्डिंग सरंध्रता बाहरी या आंतरिक रूप से प्रकट हो सकती है (जिसे अक्सर उप-सतह सरंध्रता कहा जाता है)। यह वेल्ड के एक बिंदु पर या पूरी लंबाई में भी विकसित हो सकता है, जिसके परिणामस्वरूप वेल्ड कमजोर हो जाता है।
यह जानने से कि सरंध्रता के कुछ प्रमुख कारणों की पहचान कैसे की जाए और उन्हें तुरंत कैसे हल किया जाए, गुणवत्ता, उत्पादकता और अंतिम परिणाम में सुधार करने में मदद मिल सकती है।
ख़राब परिरक्षण गैस कवरेज
खराब परिरक्षण गैस कवरेज वेल्डिंग सरंध्रता का सबसे आम कारण है, क्योंकि यह वायुमंडलीय गैसों (एन2 और एच2) को वेल्ड पूल को दूषित करने की अनुमति देता है। उचित कवरेज का अभाव कई कारणों से हो सकता है, जिनमें खराब परिरक्षण गैस प्रवाह दर, गैस चैनल में रिसाव, या वेल्ड सेल में बहुत अधिक वायु प्रवाह शामिल है, लेकिन यह इन्हीं तक सीमित नहीं है। यात्रा की बहुत तेज़ गति भी दोषी हो सकती है।
यदि किसी ऑपरेटर को संदेह है कि खराब प्रवाह समस्या का कारण बन रहा है, तो दर पर्याप्त है यह सुनिश्चित करने के लिए गैस प्रवाह मीटर को समायोजित करने का प्रयास करें। उदाहरण के लिए, स्प्रे ट्रांसफर मोड का उपयोग करते समय, 35 से 50 क्यूबिक फीट प्रति घंटा (सीएफएच) प्रवाह पर्याप्त होना चाहिए। उच्च एम्परेज पर वेल्डिंग के लिए प्रवाह दर में वृद्धि की आवश्यकता होती है, लेकिन यह महत्वपूर्ण है कि दर को बहुत अधिक निर्धारित न किया जाए। इसके परिणामस्वरूप कुछ बंदूक डिज़ाइनों में अशांति हो सकती है जो परिरक्षण गैस कवरेज को बाधित करती है।
यह ध्यान रखना महत्वपूर्ण है कि अलग-अलग डिज़ाइन की गई बंदूकों में अलग-अलग गैस प्रवाह विशेषताएँ होती हैं (नीचे दो उदाहरण देखें)। शीर्ष डिज़ाइन के लिए गैस प्रवाह दर का "मीठा स्थान" नीचे के डिज़ाइन की तुलना में बहुत बड़ा है। वेल्डिंग इंजीनियर को वेल्ड सेल स्थापित करते समय इस पर विचार करने की आवश्यकता होती है।
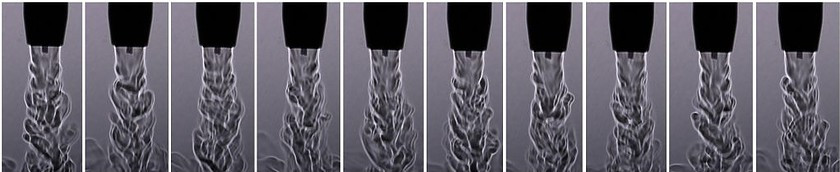
डिज़ाइन 1 नोजल आउटलेट पर सुचारू गैस प्रवाह दिखाता है
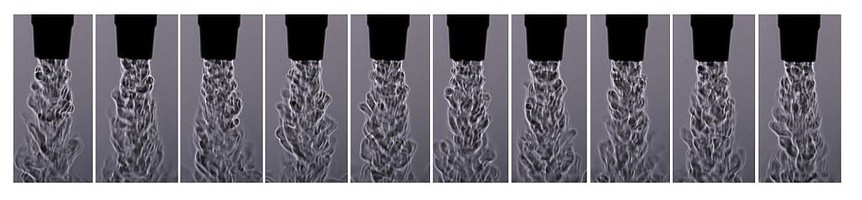
डिज़ाइन 2 नोजल आउटलेट पर अशांत गैस प्रवाह दिखाता है।
गैस नली, फिटिंग और कनेक्टर्स के साथ-साथ एमआईजी वेल्डिंग गन के पावर पिन पर ओ-रिंग्स की क्षति की भी जांच करें। आवश्यकतानुसार बदलें.
वेल्ड सेल में ऑपरेटरों या भागों को ठंडा करने के लिए पंखे का उपयोग करते समय, ध्यान रखें कि वे सीधे वेल्डिंग क्षेत्र पर केंद्रित न हों, जहां वे गैस कवरेज को बाधित कर सकते हैं। बाहरी वायु प्रवाह से बचाने के लिए वेल्ड सेल में एक स्क्रीन लगाएं।
यह सुनिश्चित करने के लिए रोबोटिक अनुप्रयोगों में प्रोग्राम को दोबारा स्पर्श करें कि टिप-टू-वर्क की उचित दूरी है, जो चाप की वांछित लंबाई के आधार पर आम तौर पर ½ से 3/4 इंच होती है।
अंत में, यदि सरंध्रता बनी रहती है तो यात्रा की गति धीमी करें या बेहतर गैस कवरैग के साथ विभिन्न फ्रंट-एंड घटकों के लिए एमआईजी बंदूक आपूर्तिकर्ता से परामर्श लें
आधार धातु संदूषण
बेस मेटल संदूषण सरंध्रता उत्पन्न होने का एक अन्य कारण है - तेल और ग्रीस से लेकर मिल स्केल और जंग तक। नमी भी इस असंतोष को प्रोत्साहित कर सकती है, खासकर एल्यूमीनियम वेल्डिंग में। इस प्रकार के संदूषक आम तौर पर बाहरी सरंध्रता का कारण बनते हैं जो ऑपरेटर को दिखाई देता है। गैल्वेनाइज्ड स्टील में उपसतह सरंध्रता का खतरा अधिक होता है।
बाहरी सरंध्रता से निपटने के लिए, वेल्डिंग से पहले आधार सामग्री को अच्छी तरह से साफ करना सुनिश्चित करें और धातु-कोर वेल्डिंग तार का उपयोग करने पर विचार करें। इस प्रकार के तार में ठोस तार की तुलना में डीऑक्सीडाइज़र का स्तर अधिक होता है, इसलिए यह आधार सामग्री पर किसी भी शेष संदूषक के प्रति अधिक सहनशील होता है। इन्हें और किसी भी अन्य तार को हमेशा पौधे के समान या उससे थोड़ा अधिक तापमान वाले सूखे, साफ क्षेत्र में रखें। ऐसा करने से संक्षेपण को कम करने में मदद मिलेगी जो वेल्ड पूल में नमी ला सकता है और सरंध्रता का कारण बन सकता है। तारों को ठंडे गोदाम में या बाहर न रखें।
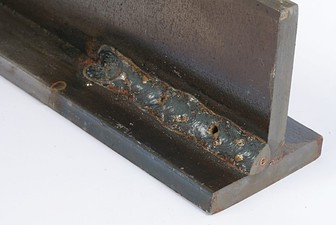
जमने के दौरान गैस फंसने से बनने वाली सरंध्रता, कैविटी-प्रकार की असंततता, एमआईजी वेल्डिंग में एक सामान्य लेकिन बोझिल दोष है और इसके कई कारण हैं।
गैल्वेनाइज्ड स्टील की वेल्डिंग करते समय, स्टील के पिघलने की तुलना में जस्ता कम तापमान पर वाष्पीकृत हो जाता है, और तेज यात्रा गति के कारण वेल्ड पूल जल्दी से जम जाता है। यह स्टील में जिंक वाष्प को फँसा सकता है, जिसके परिणामस्वरूप सरंध्रता हो सकती है। यात्रा की गति की निगरानी करके इस स्थिति का मुकाबला करें। फिर से, विशेष रूप से डिज़ाइन किए गए (फ्लक्स फॉर्मूला) धातु-कोर तार पर विचार करें जो वेल्डिंग पूल से जस्ता वाष्प को बाहर निकालने में मदद करता है।
बंद और/या छोटे आकार के नोजल
बंद और/या छोटे नोजल भी सरंध्रता का कारण बन सकते हैं। वेल्डिंग के छींटे नोजल में और संपर्क टिप और डिफ्यूज़र की सतह पर जमा हो सकते हैं, जिससे परिरक्षण गैस का प्रवाह प्रतिबंधित हो सकता है या यह अशांत हो सकता है। दोनों ही स्थितियाँ वेल्ड पूल को अपर्याप्त सुरक्षा के साथ छोड़ देती हैं।
इस स्थिति को जटिल बनाने वाला एक नोजल है जो अनुप्रयोग के लिए बहुत छोटा है और अधिक और तेजी से छींटे जमा होने की अधिक संभावना है। छोटे नोजल बेहतर संयुक्त पहुंच प्रदान कर सकते हैं, लेकिन गैस प्रवाह के लिए अनुमत छोटे क्रॉस-अनुभागीय क्षेत्र के कारण गैस प्रवाह में बाधा भी डालते हैं। संपर्क टिप से नोजल स्टिकआउट (या रिसेस) के परिवर्तन को हमेशा ध्यान में रखें, क्योंकि यह एक अन्य कारक हो सकता है जो आपके नोजल चयन के साथ गैस प्रवाह और सरंध्रता को प्रभावित करता है।
इसे ध्यान में रखते हुए, सुनिश्चित करें कि नोजल अनुप्रयोग के लिए पर्याप्त बड़ा है। आमतौर पर, बड़े तार आकार का उपयोग करके उच्च वेल्डिंग करंट वाले अनुप्रयोगों के लिए बड़े बोर आकार वाले नोजल की आवश्यकता होती है।
अर्ध-स्वचालित वेल्डिंग अनुप्रयोगों में, समय-समय पर नोजल में वेल्डिंग छींटे की जांच करें और वेल्डर प्लायर्स (वेलपर्स) का उपयोग करके हटा दें या यदि आवश्यक हो तो नोजल को बदल दें। इस निरीक्षण के दौरान, पुष्टि करें कि संपर्क टिप अच्छी स्थिति में है और गैस डिफ्यूज़र में स्पष्ट गैस पोर्ट हैं। ऑपरेटर एंटी-स्पैटर कंपाउंड का भी उपयोग कर सकते हैं, लेकिन उन्हें ध्यान रखना चाहिए कि नोजल को कंपाउंड में बहुत दूर या बहुत लंबे समय तक न डुबाएं, क्योंकि कंपाउंड की अत्यधिक मात्रा परिरक्षण गैस को दूषित कर सकती है और नोजल इन्सुलेशन को नुकसान पहुंचा सकती है।
रोबोटिक वेल्डिंग ऑपरेशन में, स्पैटर बिल्डअप से निपटने के लिए नोजल क्लीनिंग स्टेशन या रीमर में निवेश करें। यह परिधीय उत्पादन में नियमित रुकावट के दौरान नोजल और डिफ्यूज़र को साफ करता है ताकि यह चक्र समय को प्रभावित न करे। नोजल सफाई स्टेशनों का उद्देश्य एक एंटी-स्पैटर स्प्रेयर के साथ मिलकर काम करना है, जो सामने के घटकों पर यौगिक की एक पतली परत लागू करता है। बहुत अधिक या बहुत कम एंटी-स्पैटर द्रव के परिणामस्वरूप अतिरिक्त सरंध्रता हो सकती है। नोजल की सफाई प्रक्रिया में एयर ब्लास्ट जोड़ने से उपभोग्य सामग्रियों से ढीले छींटों को साफ करने में भी मदद मिल सकती है।
गुणवत्ता एवं उत्पादकता बनाए रखना
वेल्डिंग प्रक्रिया की निगरानी करने और सरंध्रता के कारणों को जानने से, समाधान लागू करना अपेक्षाकृत सरल है। ऐसा करने से अधिक आर्क-ऑन समय, गुणवत्तापूर्ण परिणाम और उत्पादन के माध्यम से अधिक अच्छे भागों को सुनिश्चित करने में मदद मिल सकती है।
पोस्ट करने का समय: फ़रवरी-02-2020